HERE IS HOW INNOVATION IMPACTS THE CONSTRUCTION WORKFORCE SHORTAGE CRISIS
_format(webp)%20(4).avif)
Dextall's digital system
Capable of eliminating up to 24 months of project design coordination and construction inefficiencies – gives client stakeholders the advantage of end-to-end project cost analysis for the entire building lifecycle, starting with the earliest design stages that tap instantly into bill of materials level architecture and building detail. Dextall’s prefabricated unitized exterior walls are installed 80% faster compared with traditional onsite construction processes resulting in improved construction schedules.
Dextall precision-manufactured structural wall panels – complete with windows and cladding – plug-and-play together with dry perimeter gaskets, eliminating the need to wet-seal the wall panels once they are set in place, which also makes scaffolding and other suspended platforms unnecessary. Dextall’s industrialized design, engineering, fabrication and installation process eliminates jobsite waste, drastically improves finished product quality, lowering embodied carbon impacts and further reducing hauling and unused materials costs.
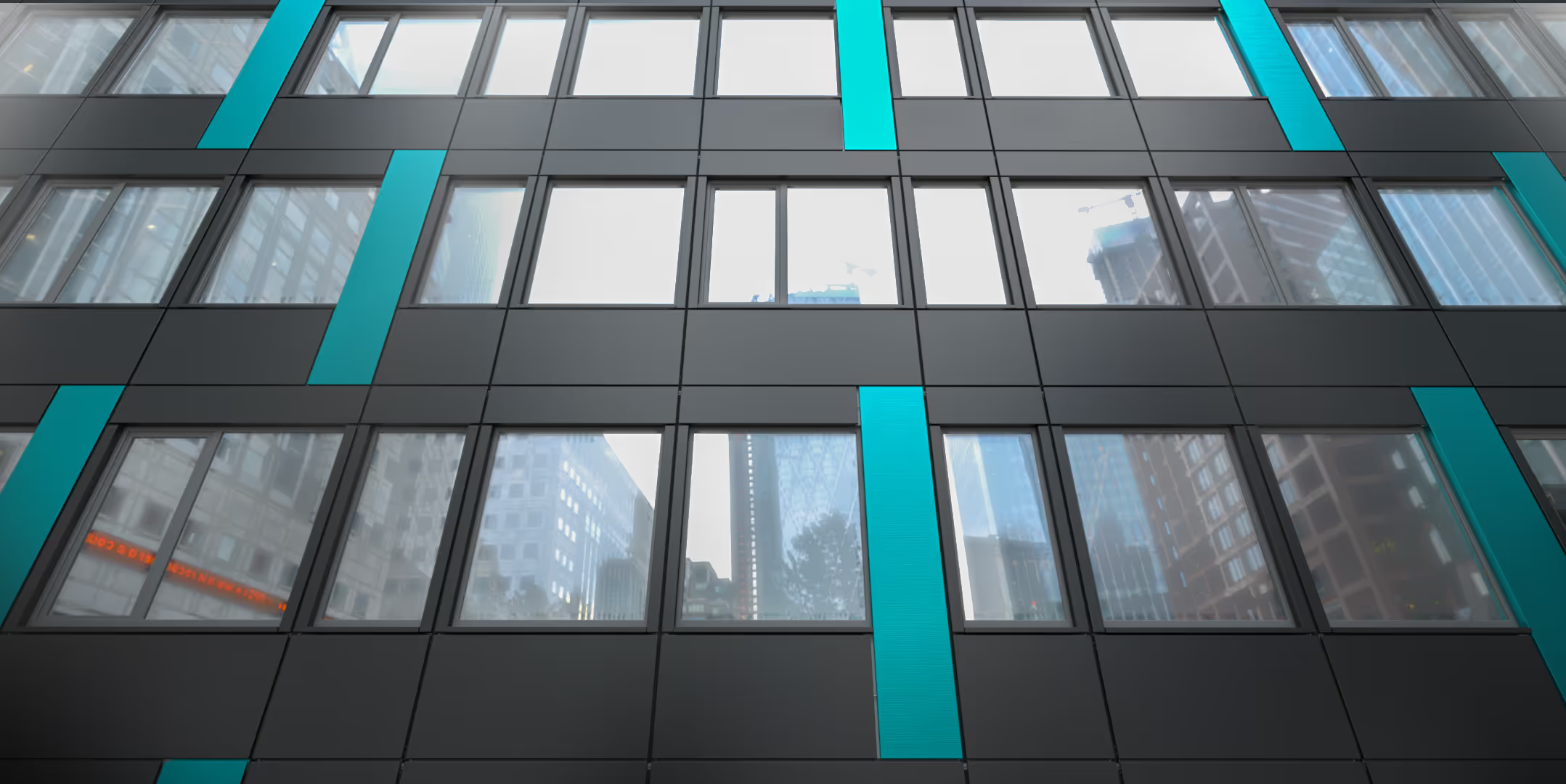
Dextall's 5 impacts on construction labor capability
Briefly, Dextall impacts labor constraint first by lowering barriers – i.e. the number of skilled worker-hours, the amount of construction-cycle time, etc. – and, at the same time, raising the capability level of fewer crew members. Installing Lego-like, precision-manufactured exterior panels achieves faster and higher quality. The result is a completed building that performs to the highest measures of durability and performance.
Specifically, here are five opportunity areas of impact on skilled labor shortages for which Dextall’s innovative design, development, materials science, engineering, fabrication, and installation systems can turn the tide of constraint, and rebalance capacity and demand.
Pre-construction
Much of Dextall’s time- and labor-saving capability occurs well in advance of work at the job site. Dextall’s architect and engineer empowering digital-twin data and design platform solves for aesthetic, performance, code compliance, and cost-and-materials availability optionality all of which effectively can shave two-years of pre-construction processes – eliminating crossed-signals and costly process delays – which add up to greater throughput with 80% savings in human work hours.
Pre-fabrication
Dextall’s precision-manufactured panel system integrates the work normally done on a jobsite by as many as seven separate skilled trade contractor crews:
- Framing contractor crew (5-10 people)
- Interior drywall installers working on exterior walls (3-5 people)
- Insulation contractor (5-10 people)
- Sheathing contractor (5-10 people)
- Window installer (10-15 people)
- Exterior cladding installer (10-15 people)
- Caulker (crew that applies silicone from the outside) (3-5 people)
- Exterior cleaning crew depending on the cladding used, finished façade sometimes needs to be cleaned, especially windows after brick installation. (3-5 people)
Installation
Instead, a Dextall site installation requires a simple crane and a six-member crew to wrap up a building exterior and make it completely water- and air-tight, about 80% faster – and with no warrantee or call-back risk — compared with traditional onsite process.
Crew-member safety
Both Dextall’s factory prefabrication conditions – eliminating bad weather impacts — and our on-site panel installation processes protect the health safety of project team members from end-to-end in the construction cycle, a critical impact on current labor capacity.
Talent attraction
Among the most important impacts innovators like Dextall exert on today’s labor capacity challenge is that by fusing manufacturing technology, digitized design and engineering, and industrialized, robotic production into its platforms, a next generation of highly capable, purpose-driven construction workforce participants.
Construction labor will never return to a time when plentiful skilled workers made themselves available at low cost. Innovation, and innovators like Dextall, can turn the tide of impact from crisis to capability.